Magnetic Connectors for Medical Device: 5 Essential Feature
It’s interesting how you might find yourself discussing the latest trends in medical technology just as you’re contemplating a project involving wearables. When you consider the demands of modern medical device, magnetic connectors stand out as an ideal choice. Their compact design, breakaway safety features, and high conductivity make them indispensable in critical applications. But what truly sets them apart is their unique ability to enhance patient safety while ensuring reliable performance. As you explore the nuances of these connectors, you may begin to see why they’re becoming a preferred option in the healthcare industry.
Key Takeaways
- Magnetic connectors enable quick and efficient connections, allowing for seamless operation in critical medical electrical snap applications.
- Their break-away function ensures immediate disconnection under tension, protecting both users and sensitive device components.
- With up to 30,000 mating cycles, these connectors offer durability and reliability, minimizing wear and tear over time.
- Waterproof and anti-corrosion features, adhering to IP67 standards, enhance device longevity and performance in challenging environments.
- Easy maintenance and cleaning capabilities contribute to improved safety and hygiene in medical settings.
Compact Design for Miniaturized Wearables
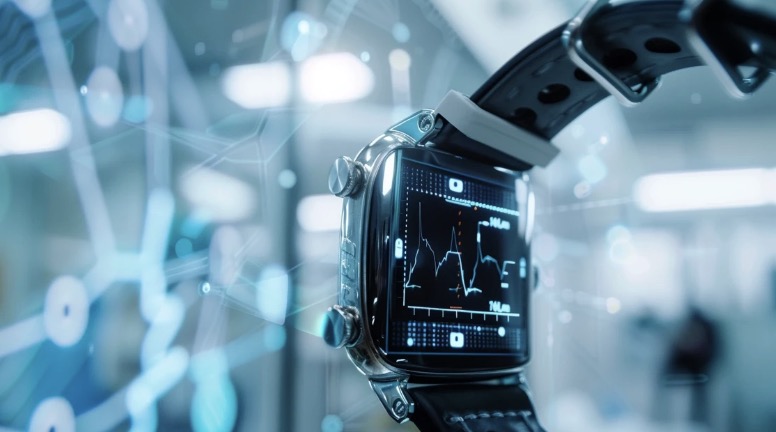
Real-time health monitoring enabled by magnetic connectors in smart wearable device.
In designing miniaturized wearables, a reduced form factor allows you to integrate components more tightly, enhancing overall device performance.
Compared to traditional mechanical connectors, magnetic connectors provide a streamlined solution that minimizes space while maintaining reliability. This compact design not only simplifies manufacturing but also improves user experience by enabling seamless connections.
How reduced form factor enables tighter device integration
How can a reduced form factor revolutionize device integration in miniaturized wearables? By using magnetic connectors, you can greatly enhance the compactness of your design. These magnetic electronic connectors provide a reliable, low-profile solution that allows for tighter integration of components, which is vital in today’s miniaturized device. The design flexibility offered by magnetic connectors enables engineers to create sleek and lightweight device without compromising functionality.
Feature | Benefits | Applications |
---|---|---|
Magnetic electronic connector | Quick and efficient connections | Wearable health monitors |
Compact design | Space-saving integration | Smartwatches |
Long lifespan | Reduced maintenance needs | Bluetooth headsets |
High reliability | Enhanced user safety | Medical device |
Low profile | Aesthetic appeal | Fitness trackers |
With magnetic connectors, you can achieve a sophisticated balance between form and function. Their ability to minimize size while maintaining performance is crucial for device like smartwatches and health monitors. This miniaturization trend not only advances technology but also improves user experience by offering seamless operation and portability.
Comparison with traditional mechanical connectors
When comparing magnetic connectors to traditional mechanical connectors, you’ll quickly notice that the former excels in several key areas, particularly in compact design for miniaturized wearables. Magnetic connectors utilize a unique mechanism that allows them to maintain a secure connection without the bulk of conventional locking systems. This reduction in size is essential for wearables, where every millimeter counts.
Moreover, the inherent alignment provided by magnetic forces simplifies the mating process, allowing for seamless connections even in tight spaces. Unlike mechanical connectors that may require precise alignment and forceful engagement, magnetic connectors enable quick, blind mating—ideal for devices that need to be attached or detached frequently.
Additionally, magnetic connectors typically feature spring-loaded contacts, which guarantee stable and reliable connections while accommodating minor misalignments. This contrasts sharply with traditional connectors, which can suffer from wear and tear due to repeated mechanical engagement.
Ultimately, magnetic connectors provide a more compact, user-friendly solution that enhances the design and functionality of miniaturized wearables, making them the preferred choice in modern medical device applications.
Breakaway Safety for Patient Comfort
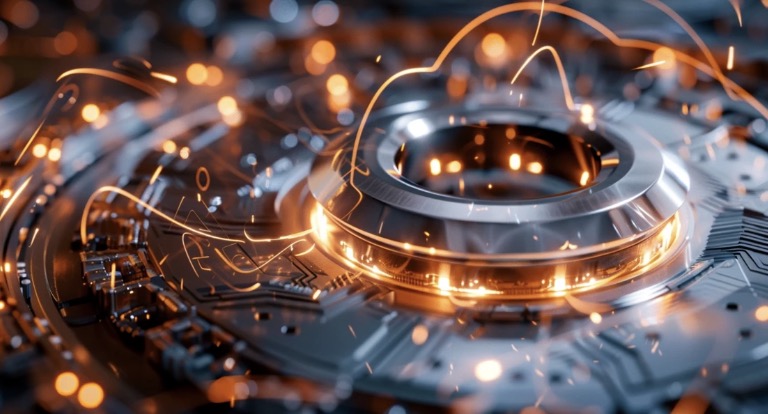
Magnetic contacts enable smooth and powerful current flow with minimal resistance.
In rehabilitation and home therapy settings, magnetic connectors play an important role in enhancing patient safety and comfort. Their breakaway feature guarantees that any unexpected tug or pull leads to a safe disconnection, preventing injuries during use. This design not only promotes confidence in the equipment but also supports seamless patient care by minimizing disruptions in therapy sessions.
Applications in rehabilitation and home therapy
Magnetic connectors play a vital role in rehabilitation and home therapy by enhancing patient safety through their breakaway functionality. In these settings, ensuring a seamless and safe connection between devices is pivotal.
When using equipment like mobility aids or therapeutic machines, the risk of accidental disconnection can pose notable dangers. Magnetic connectors mitigate this risk by allowing devices to disconnect under tension, preventing potential harm to the patient.
These connectors provide an intuitive and efficient interface, making it easy for patients or caregivers to connect and disconnect devices without requiring complex maneuvers. This functionality is particularly advantageous in home therapy environments, where simplicity can greatly enhance user experience and adherence to treatment protocols.
The quick mating and un-mating process reduces the likelihood of operator errors, ensuring consistent performance without sacrificing safety.
Furthermore, the robust design of magnetic connectors enhances durability, making them ideal for frequent use in rehabilitation settings. Patients gain confidence in their devices, knowing that the connectors will safely disengage if pulled.
Preventing injuries with magnetic separation
Many medical device now incorporate breakaway safety features that utilize magnetic separation to prevent injuries and enhance patient comfort. This innovative design allows connectors to disconnect easily under tension, minimizing the risk of harm to both patients and equipment.
When a device experiences an unexpected pull or tug, the magnetic connector disengages rather than exerting excessive force. This immediate separation protects delicate components and reduces the potential for injury during use.
In practical terms, you’ll find this technology in devices like patient monitors and therapeutic equipment, allowing for quick recovery from accidental disconnections. The magnetic force maintains a reliable connection under normal circumstances while ensuring safety when needed.
Additionally, these connectors support one-handed operation, which is vital in emergency situations where swift action is essential.
Moreover, this self-mating feature simplifies the connection process, reducing the likelihood of operator errors. By integrating magnetic separation into medical device, manufacturers enhance both safety and user experience, fostering an environment where patients feel secure during treatment.
Ultimately, this breakthrough in connector technology represents a significant advancement in medical device design, prioritizing patient safety without compromising functionality.
High Conductivity with Low Resistance
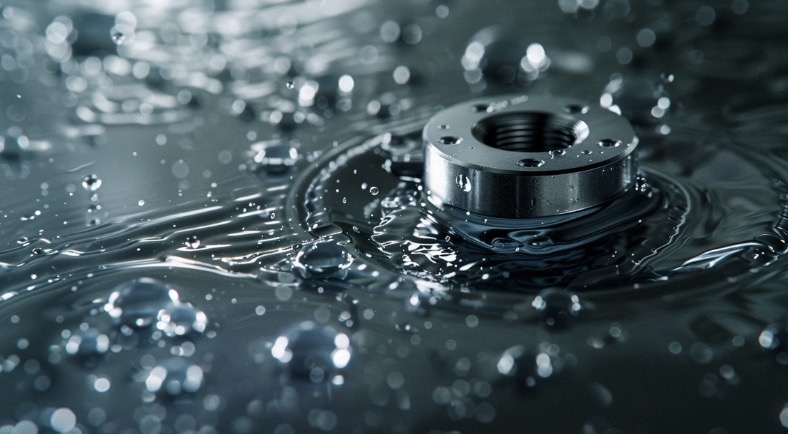
Magnetic connectors built for wet and corrosive conditions in medical environments.
When evaluating magnetic connectors, you’ll want to focus on the importance of high conductivity and low resistance. Richarms’ gold-plated contacts guarantee top performance by minimizing energy loss during transmission. Internal tests and conductivity benchmarks further confirm their superiority in maintaining reliable connections essential for medical applications.
Richarms’ gold-plated contacts
Richarms’ gold-plated contacts offer high conductivity with low impedance, ensuring peak efficiency in various applications, including medical device. By utilizing gold plating, these contacts minimize resistance, enhancing the effectiveness of power and data transmission. This is particularly vital in medical environments where reliability and accuracy can directly impact patient outcomes.
Key features of Richarms’ gold-plated contacts include:
- Enhanced Longevity: Gold resists corrosion and tarnishing, extending the lifespan of connectors.
- Superior Conductivity: Gold’s high conductivity ensures optimal signal transmission with minimal power loss.
- Low Contact Resistance: This characteristic is essential for maintaining the integrity of electrical connections, especially in sensitive medical device.
- Dependable Performance: With fewer connection failures, you can trust these contacts in demanding applications.
- Ease of Maintenance: The smooth surface of gold-plated contacts simplifies cleaning and reduces the risk of debris accumulation.
Incorporating Richarms’ gold-plated contacts into your medical device design not only enhances efficiency but also contributes to greater safety and functionality in critical healthcare settings.
Internal tests and conductivity benchmarks
Conductivity benchmarks and internal tests play an essential role in evaluating the performance of connectors in medical device, particularly concerning high conductivity and low impedance. These benchmarks enable you to assess how efficiently electrical current flows through the connectors, guaranteeing they meet strict performance standards essential for medical applications.
During internal testing, connectors are subjected to rigorous evaluations that simulate real-world conditions. You’ll find that magnetic connectors often exhibit superior conductivity due to their precision-engineered contacts and low-impedance pathways. This ensures minimal energy loss and maximizes the reliability of medical device, which is crucial in life-saving scenarios.
High conductivity correlates with improved performance, reducing the risk of overheating and maintaining signal integrity.
Furthermore, the low impedance of magnetic connectors contributes to their longevity, allowing them to endure thousands of mating cycles without significant degradation.
Waterproof and Anti-Corrosion Performance
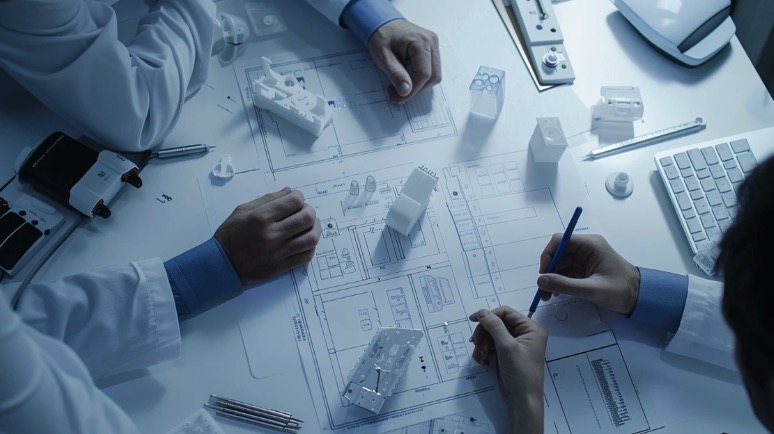
Engineering teams collaborating on magnetic connector design for medical innovations.
When designing magnetic connectors for medical device, you need to prioritize waterproof and anti-corrosion performance to guarantee reliability and longevity. Adhering to IP67 standards and utilizing advanced material coatings can greatly enhance the durability of these connectors, especially in sweat or external wearables. Understanding these specifications will help you select the right connectors for your application, guaranteeing excellent performance in challenging environments.
IP67 standards and material coatings
IP67 standards are crucial for maintaining the reliability and durability of magnetic connectors in medical device, particularly in environments where exposure to moisture and contaminants is widespread. These standards indicate that the connectors can withstand immersion in water and are dust-tight, making them ideal for the challenging conditions found in healthcare settings.
When you consider the performance of magnetic connectors, focus on the following aspects:
- Waterproofing: Ensures device safety during cleaning or accidental spills.
- Corrosion Resistance: Coatings protect against chemical exposure, extending connector life.
- Durability: High-quality materials withstand frequent use, minimizing wear and tear.
- Reliability: Consistent performance in diverse environments enhances device functionality.
- Ease of Maintenance: IP67-rated connectors simplify cleaning and sterilization processes.
The material coatings used in these connectors contribute significantly to their performance. By utilizing advanced coatings, you enhance their resistance to both water and corrosive substances, guaranteeing that your medical device remain operational and safe for patient use.
Adhering to IP67 standards, magnetic connectors withstand the rigorous demands of medical applications, providing peace of mind for manufacturers and healthcare providers alike.
Use cases in sweat/external wearables
The performance of magnetic connectors in sweat and external wearables greatly benefits from strong waterproof and anti-rust features. These characteristics are vital for devices like fitness trackers and smartwatches, which are often exposed to moisture and sweat. By utilizing high-quality materials and coatings, magnetic connectors resist rust, ensuring long-term reliability and functionality in challenging environments.
Waterproof ratings, such as IP68, guarantee that these connectors can endure submersion in water, making them ideal for wearables used during intense workouts or in humid conditions. This level of protection not only enhances user experience but also extends the lifespan of the device. Additionally, the magnetic connection allows for quick and secure attachment, minimizing wear on the connector itself.
The spring-loaded design further guarantees a consistent connection, compensating for any movement during activities. This stability is essential in maintaining accurate data transmission for health monitoring applications. Moreover, easy disconnection under stress prevents damage to both the device and the user, aligning with safety protocols.
To summarize, waterproof and anti-rust capabilities make magnetic connectors essential in the development of sweat and external wearables.
Fast Prototyping & OEM Support from Richarms
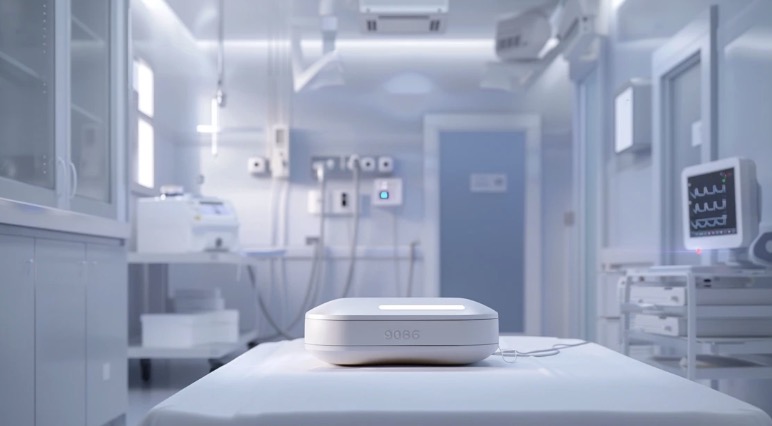
Magnetic connectors improve safety and hygiene in clinical-grade medical device.
When you engage with Richarms, you benefit from a streamlined 3D sample flow that speeds up your prototyping process. Their engineering co-development services guarantee that your specific needs are met, enabling efficient customization tailored to your project.
Additionally, their minimum order quantity (MOQ) flexibility supports both small and large-scale production, facilitating a smooth shift from concept to final product.
3D sample flow & engineering co-development
Rapid prototyping and OEM support from Richarms streamline the sample flow and engineering co-development process, optimizing quick turnaround times and enhanced collaboration. This approach allows you to effectively develop and refine product designs, especially in the context of medical device, where precision and reliability are paramount.
- Accelerated design iterations minimize time to market.
- Access to expert guidance facilitates best design choices.
- Seamless integration of feedback improves product performance.
- Cost-effective solutions reduce overhead and enhance scalability.
- Enhanced communication fosters teamwork and innovation.
With Richarms, you can expect a structured process that prioritizes efficiency. Their commitment to rapid prototyping means you’ll receive initial samples swiftly, allowing for immediate testing and validation. Moreover, their OEM support ensures you have the resources necessary for both small-scale and large-scale production.
You’ll benefit from a collaborative environment where engineers and designers work closely together, addressing challenges head-on. By leveraging advanced technologies and materials, Richarms empowers you to create medical device that meet stringent industry standards, ultimately improving patient care and safety. This integrated approach to sample flow and co-development lays the foundation for successful product realization.
MOQ and customization process overview
Understanding the minimum order quantity (MOQ) along with the customization process is essential for efficient collaboration with Richarms, especially in the fast-paced medical device sector. The MOQ varies based on specific connector types and configurations, enabling you to balance production needs with budget constraints. Typically, Richarms offers flexible MOQs, accommodating both small-scale prototypes and larger production runs.
The customization process at Richarms is streamlined to facilitate rapid prototyping. Once you’ve defined your requirements, the engineering team collaborates closely with you to refine designs. You can expect a development timeline of 3-5 working days for initial prototypes, ensuring swift feedback loops.
Richarms provides OEM support, allowing you to tailor magnetic connectors that meet precise specifications and compliance standards relevant to medical applications. Throughout this process, clear communication is prioritized, ensuring you stay informed and involved at every stage.
Conclusion: Should You Use Magnetic Connectors for Your Medical Product?
When considering magnetic connectors for your medical product, evaluate key factors such as reliability, ease of use, and maintenance requirements.
These connectors offer benefits like reduced wear and tear, enhanced cleaning efficiency, and improved patient safety.
To explore how magnetic connectors can meet your specific needs, get a custom quote or sample pack today.
Summary checklist for engineers
Evaluating the integration of magnetic connectors in your medical product design is crucial for ensuring optimal functionality and safety. As you consider incorporating these advanced connectors, it helps to have a checklist to guide your decision-making process.
- Compatibility: Confirm the magnetic connectors align with your device’s specifications and operational requirements.
- Durability: Seek connectors with a long life span (up to 30,000 mating cycles) to minimize maintenance needs and downtime.
- Safety Features: Prioritize designs with a break-away function to prevent injury during accidental disconnections.
- Ease of Use: Evaluate the connectors for one-handed operation capabilities, facilitating quick and safe user interactions.
- Maintenance: Assess how these connectors contribute to efficient cleaning and sterilization processes, reducing the risk of contamination.
Get a custom quote or sample pack today
Integrating magnetic connectors into your medical product design can greatly enhance functionality, safety, and user experience. These connectors streamline the connection process while ensuring high reliability, making them suitable for critical applications. If you’re considering magnetic connectors, now’s the time to act.
Here’s a quick comparison to help you decide:
Feature | Magnetic Connectors |
---|---|
Connection Ease | Quick, one-handed operation |
Durability | Up to 30,000 mating cycles |
Safety | Break-away function prevents injury |
By choosing magnetic connectors, you’re investing in a solution that minimizes wear, enhances cleanliness, and simplifies maintenance. The design’s focus on preventing damage from unintended disconnections is especially critical in medical settings.
Ready to elevate your medical device with magnetic connectors? Get a custom quote or sample pack today. With tailored solutions designed to meet your specific needs, you’ll find the perfect match for your product. Don’t compromise on quality; make the smart choice in connector technology. Reach out now to see how magnetic connectors can revolutionize your medical device design.
Frequently Asked Questions
How Do Magnetic Connectors Reduce Cleaning and Maintenance Efforts?
Magnetic connectors minimize cleaning efforts by reducing exposed parts, preventing debris accumulation, and simplifying disconnection for sanitization. Their design enhances durability and supports efficient maintenance, ensuring quick, reliable connections without compromising hygiene standards.
Can Magnetic Connectors Be Customized for Specific Medical Applications?
Yes, you can customize magnetic connectors for specific medical applications. By adjusting dimensions, polarity, and interface types, you enhance functionality and guarantee compatibility with unique equipment, improving operational efficiency and patient safety in medical environments.
What Materials Are Used in Magnetic Connectors for Medical Device?
Magnetic connectors often utilize high-temperature thermoplastics and neodymium magnets, ensuring durability and reliability. With up to 30,000 mating cycles, these materials enhance longevity, making them ideal for demanding medical applications and frequent use.
How Do Magnetic Connectors Impact the Overall Design Flexibility of Devices?
Magnetic connectors enhance your device’s design flexibility by allowing compact configurations and minimizing space requirements. They enable quick connections, streamline assembly processes, and support innovative layouts, ultimately promoting more efficient and versatile device designs tailored to user needs.
Are Magnetic Connectors Compatible With Existing Medical Device Standards?
Yes, magnetic connectors can be compatible with existing medical device standards. They often meet safety, reliability, and performance criteria, allowing for efficient integration into various devices while enhancing cleaning, maintenance, and overall functionality in medical environments.
Conclusion
In the domain of medical device, opting for magnetic connectors isn’t just a choice; it’s a commitment to safety and efficiency. With their compact design, breakaway functionality, and robust performance, these connectors meet the demands of modern healthcare. As you weigh your options, consider: can you afford to compromise on reliability? Embracing magnetic connectors could elevate your product, ensuring it not only meets industry standards but also enhances patient care. The future of medical connectivity is magnetic—are you ready to connect?